First, folding cartons
The carton is a very important sales package. It mainly plays a role in beautifying goods, promoting sales, increasing the added value of goods, and facilitating portability. It also serves the function of protecting the goods. Cartons are usually whiteboard, cardboard, and teaboard paper, and are directly printed and decorated to form a box.
The carton can be divided into a folding carton and a fixed carton according to its structure. The biggest difference between folding cartons and fixed cartons is that folding cartons can generally be folded into flat sheets for stacking, transportation and storage before they are shipped. They are folded and assembled when used. The fixed cartons must be stapled or glued and must not be folded. Folding cartons are one of the most widely used and most versatile merchandise sales packaging containers. They are widely used in the packaging of food, medicine, electronic products and cosmetics.
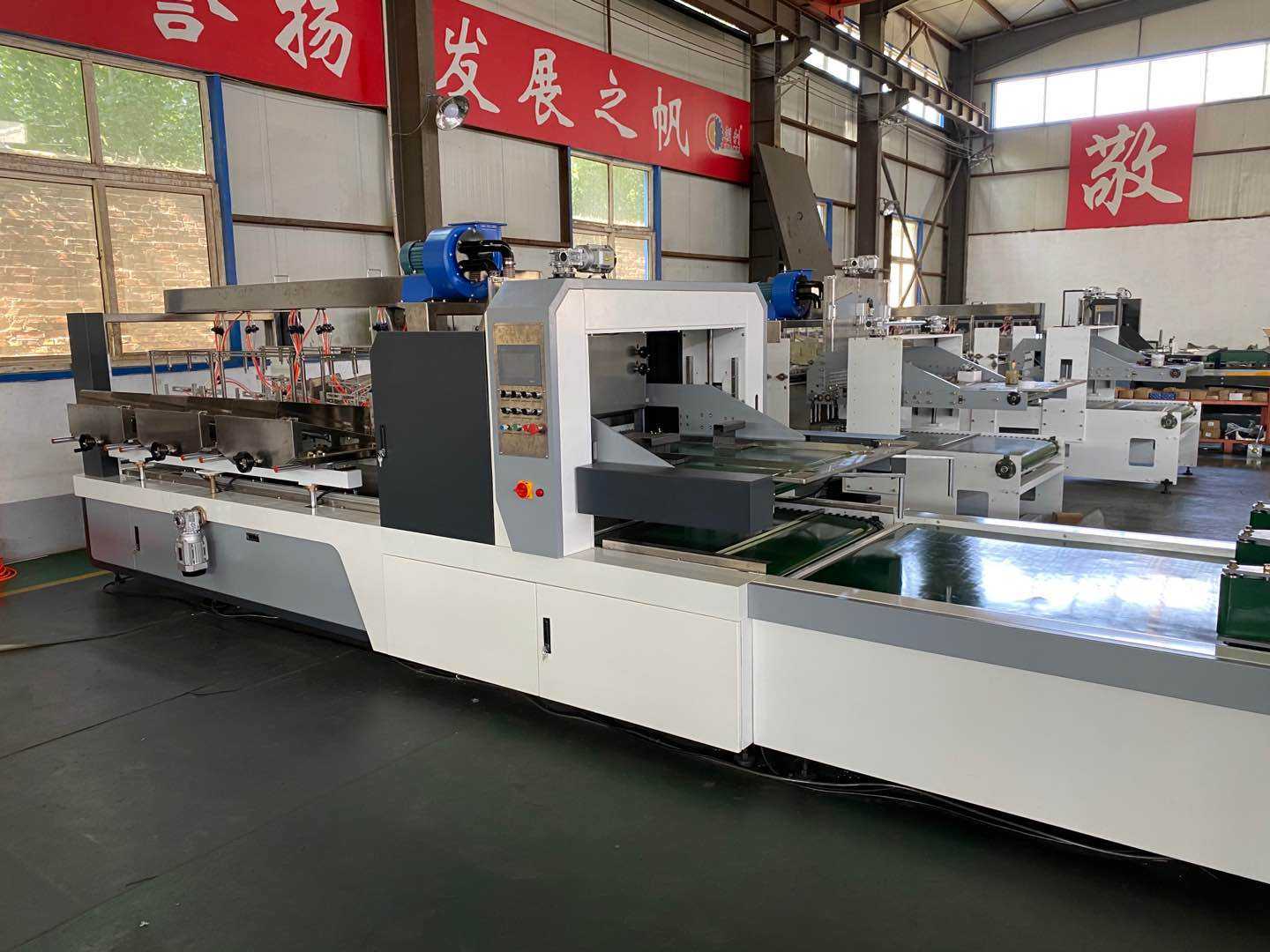
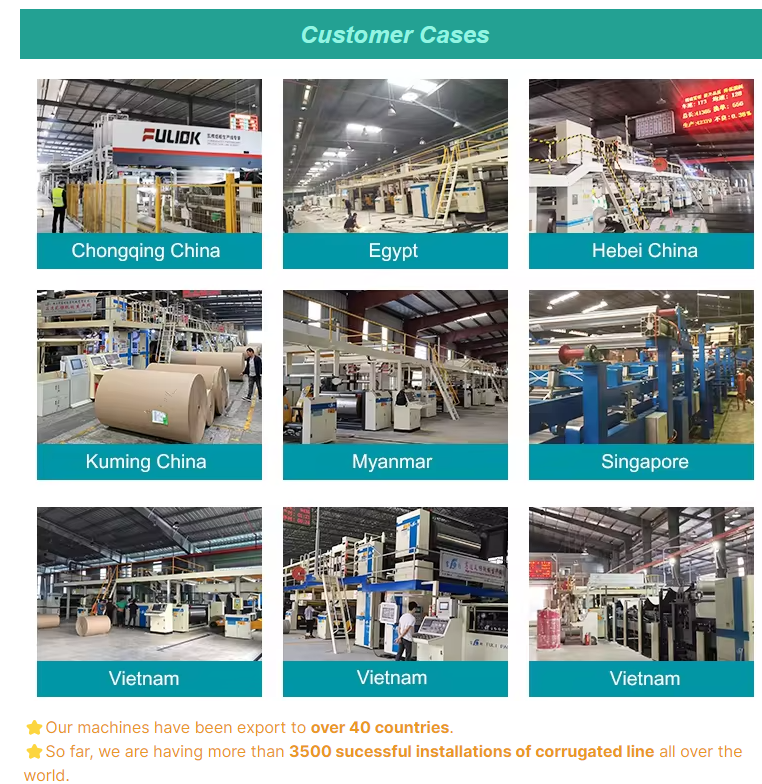
Second, the status of screen printing in the field of special effects folding carton printing
Currently in the field of domestic folding carton printing, offset, gravure, flexo, screen printing and other printing methods coexist, each with its own characteristics. The large-volume folding cartons generally need to complete the processes of printing, die-cutting, and indentation at one time, and are suitable for online printing using a web printing press. Flexo printing allows a variety of processes to operate online, to achieve the front input roll materials, back-end output box, flexo printing using water-based ink, non-toxic, non-polluting, in line with current environmental protection requirements, in the folding carton printing market has obvious advantages .
Screen Printing Due to the thick ink layer, rich graphic layers, strong three-dimensional impression, and wide range of printing materials, the use of coarse-grained special inks to achieve special decorative effects (such as matte, ice, refraction, wrinkles, etc.) can greatly stimulate consumers. Purchasing desire to enhance the added value of goods. The field of special effect folding carton printing will still have some room for development.
Traditional platform screen printers use manual feeding and ink supply, slow printing speed, low production efficiency, large material consumption, and difficult to control quality, making it difficult to meet the need for high-volume cartons such as cigarette packs.
Web rotary screen printing uses a nickel metal rotary screen plate, a built-in squeegee and an automatic ink supply system. The squeegee transfers the printing ink from the rotary screen to the surface of the substrate supported by the impression cylinder. The entire printing process from paper feeding, ink supply, printing registration to UV drying, etc. are fully controlled by the computer. The circular screen printing plate is made of 100% nickel non-woven material and is electroformed. The mesh is hexagonal and the entire mesh surface is even and thin to ensure the stability and precision of the imprinting. Due to the high speed of the high-speed rotary screen printing line (up to 125m/min), high production efficiency, stable quality of the printed product, and low consumption, it changed the way of manual feeding and ink supply for traditional flat-press screen printing machines. Automatic, large-scale mass production of fine folding cartons.
Roll web screen printing machine can not only meet the requirements of special effects such as printing frosting and ice flower, but also can be used for hot stamping holographic anti-counterfeit labels, embossing, and die-cutting molding. It is easy to realize high-speed automatic printing paper boxes.
Third, combination printing will become the ideal way for folding carton printing
Combined printing refers to a flow production line made up of various types of printing and finishing machines. Combination printing will be the ideal way for carton printing. For example, the CTlasus Rcs 330, the latest generation of combined printing equipment from the Galllas Group, consists of four UV flexographic printing units and two screen printing units. Modern control and advanced servo technology make UV flexo printing, rotary screen printing, UV glazing, and roll-to-reel die cutting combine to automatically complete the printing and packaging of color boxes.
Fourth, folding carton screen printing process points
Printing technology is a systematic project, which is mainly divided into three major processes: prepress, printing, and postpress. Each process must be taken seriously in order to produce high quality carton products.
1. Application of computer design to ensure the accuracy of box making
In the design process of the packaging carton, we must first select the appropriate carton model according to the needs of the commodity packaging. If the conventional model can not meet the requirements, we must design a new model according to the specific characteristics of the goods, and then draw an accurate box. The correctness of the drawings, the box structure and the accuracy of the box shape determine the final quality of the carton. At present, computer-aided design (CAD) and computer-aided manufacturing (CAM) are widely used in advanced countries in the world. When designing the packaging carton, according to the user's requirements, the computer can select the packaging materials, corrugated paper type, appearance size and style, and adopt the man-machine dialogue operation mode to design the carton box structure, the discharging scheme, the printing decoration pattern, etc. Quickly draw the outlines of the printing, backing processing, and the die-cutting of the cassette. So far, hundreds of "carton system CAD/CAM" systems have been introduced abroad. The use of computer-designed packaging boxes not only shortens the production cycle, but also ensures the accuracy. This has created conditions for the computer-aided manufacturing of carton boxes and the automation of post-printing processes such as printing, bronzing, die-cutting and gluing. China Founder Founder successfully developed the Founder packaging system and launched a professional software for the structural design of the box - Founder Pack. Peking University Founder packaging system includes a number of functions such as packaging structure design, layout production, appearance display, and die cutting data generation. Founder packaging system can accurately control all aspects of packaging design, production and processing with all-digital means.
The CAD system box library developed by the Graphic Center of Beijing Institute of Graphic Arts reflects the convenience, accuracy and openness characteristics.
2, the application of decorative ink, improve the color box grade
Decorative inks are inks that produce imitation metal etching (scrused), refraction, wrinkles, ice flowers, and other decorative patterns after printing on gold, silver cardboard, and certain colored cardboards. They are non-colored inks. Has been widely used in printing tobacco, wine, cosmetics and other packaging. Since the effects of imitating metal etching (sandwiching), lathing, and refraction must be instantaneously cured, they can only be printed using UV inks (UV curable inks) (curing in 3 to 5 seconds). Although wrinkles and ice flowers cure slowly, they can only produce the desired effect by controlling UV curing conditions.
3. The use of UV/EB combined with new drying methods to avoid the occurrence of discoloration and deformation of the printed products. Normal drying is one of the keys to ensure the quality of printing and glazing. The role of the drying device is to quickly dry and consolidate the ink and coating on the print to prevent the print from sticking and sticking. UV drying treatment has good effect on the surface layer curing, but Flexo Printer Slotter cannot achieve the effect of penetrating or curing a thick film-forming glazing coating in time on the high speed coating production line. At the same time, only 20% of the energy actually consumed is converted into ultraviolet light to generate a curing effect. Another 60% of the electricity is released as heat, and the remaining 20% is converted into visible light and is wasted.
Recently, foreign developed countries have applied the electron beam (EB) processing technology originally used for mechanical processing to high-efficiency printing production. Electron beam drying has become a new type of energy conversion processing method. Electron beams (EBs) generate agglomerated, dense, directional electron flow through electrical vacuum devices. When the electron beam impinges on the workpiece, the kinetic energy becomes thermal energy, and the energy generated allows the ink and the varnish coating to be maximally cross-linked and polymerized without post-cure and solvent residue. A new drying method using a combination of UV/EB (UV and EB), low-energy, low-heat UV light can cure the coating surface, and the depth of the coating is dried by the electron beam. The solidification of the surface layer and the deep layer is completed at the same time, and no color-printing phenomenon occurs, and the heat shrinkage deformation of the coating is avoided.
4. Post-press processing is an important means to realize the value-added of printed products. Post-press processing is an important means to ensure the quality of printed products and realize value-added. Especially for packaging and printing products, many of them use post-press processing technology to greatly improve quality and increase its value. Special features. In a sense, post-press processing is the key to determining the success or failure of printed matter. Often, due to the quality problems of post-press processing, the printed matter has to be abandoned. For example, a beautifully printed box (box) cannot be boxed because of a die cutting error.
Polishing or laminating, hot stamping, embossing and embossing are the three most commonly used decorative methods for paper packaging. Die cutting, creasing, and pasting are the processing methods for carton forming.
(1) Polishing
The so-called glazing is a process in which a colorless and transparent coating is applied on the surface of a print to form a glossy film. During the coating process, the leveling of the coating on the surface of the printed product enhances the smoothness of the surface of the printed product, not only improves the surface gloss of the printed product, but also improves the surface properties of the printed product, and plays a role in protecting the printed graphic.
Polishing can be done with waterborne varnish, alcohol soluble varnish, and UV varnish. The first two varnish coats use infrared drying, and the latter varnish requires UV drying. At present, the coating glazing at home and abroad mainly uses UV coating and water-based coating.
(2) Covered film
The cover film is a transparent plastic film (multi-purpose BOPP film) which is applied to the surface of the printed product by hot pressing to protect and increase the gloss. The printed product is covered with a plastic film on the surface, which has the functions of friction resistance, moisture resistance, light resistance, waterproofness and anti-fouling. It not only protects the printed matter, prolongs its service life, but also improves the print quality. Ornamental. If the compound is a transparent light film, Auto Glue Applying Machine will make the print dazzling, flexo plate making machine looks magnificent; if the compound is a matte film, carton machine spare parts will give people a simple, elegant feel, greatly increasing the artistic charm of the print.
(3) hot stamping, embossing
Because the bronzing has a unique metallic luster and a strong visual effect, the decorated product is extraordinarily luxurious and magnificent. Therefore,Corrugated Line Glue Machine is a process often used for commodity packaging.
Electro-aluminum consists of a base film layer, a release layer (release coating), a color coating, a metal coating (aluminized layer), and an adhesive layer.
The hot stamping foil actually consists of two main thin layers, the polyester film base and the transfer layer. In the hot stamping process, the hot stamping layer is impressed on all or part of the surface of the substrate by means of heat and pressure. When the hot stamping is completed, the polyester film is pulled together with the parts that have not been transferred. Embossing, also known as embossing and embossing, is a processing method that uses a pair of concavo-convex patterns to print a print out of embossed images without printing ink.
This method is mostly used for the processing of printed matters such as trademarks, paper boxes, greeting cards, and bottle stickers. The effect is vivid and beautiful, and the three-dimensional effect is strong.
The process of embossing is gravure printing → stamping and embossing. Hot stamping and embossing are the most commonly used methods for color box decoration. In recent years, there have been some new trends in bronzing and embossing processes in China. With the improvement of the processing level of bronzing foils and bronzing plates and the use of new machinery and equipment, high-speed bronzing (flattening speed > 5000 sheets/h), positioning bronzing, three-dimensional bronzing (bronzing and embossing one-time finishing) and bronzing surfaces Printing and other technologies have begun to be applied to the production of cartons in China, and the level of technology is rapidly approaching international standards.
1 positioning hot stamping
High-end products In order to make the holographic logo hot stamping can produce better anti-counterfeiting effect, most of them use independent pattern holographic logo stamping. In other words, the holographic logo on the galvanized aluminum is made into a separate trademark pattern, and there is an alignment mark next to each pattern. This requires the hot stamping device to have both a position identification system and a positioning stamping accuracy of ±0.5. Within mm. Due to the features of intuitive holographic marking and high technical difficulty, the holographic logo of the independent pattern has so far been the best means of anti-counterfeiting for packaging. Bobst hot stamping machine